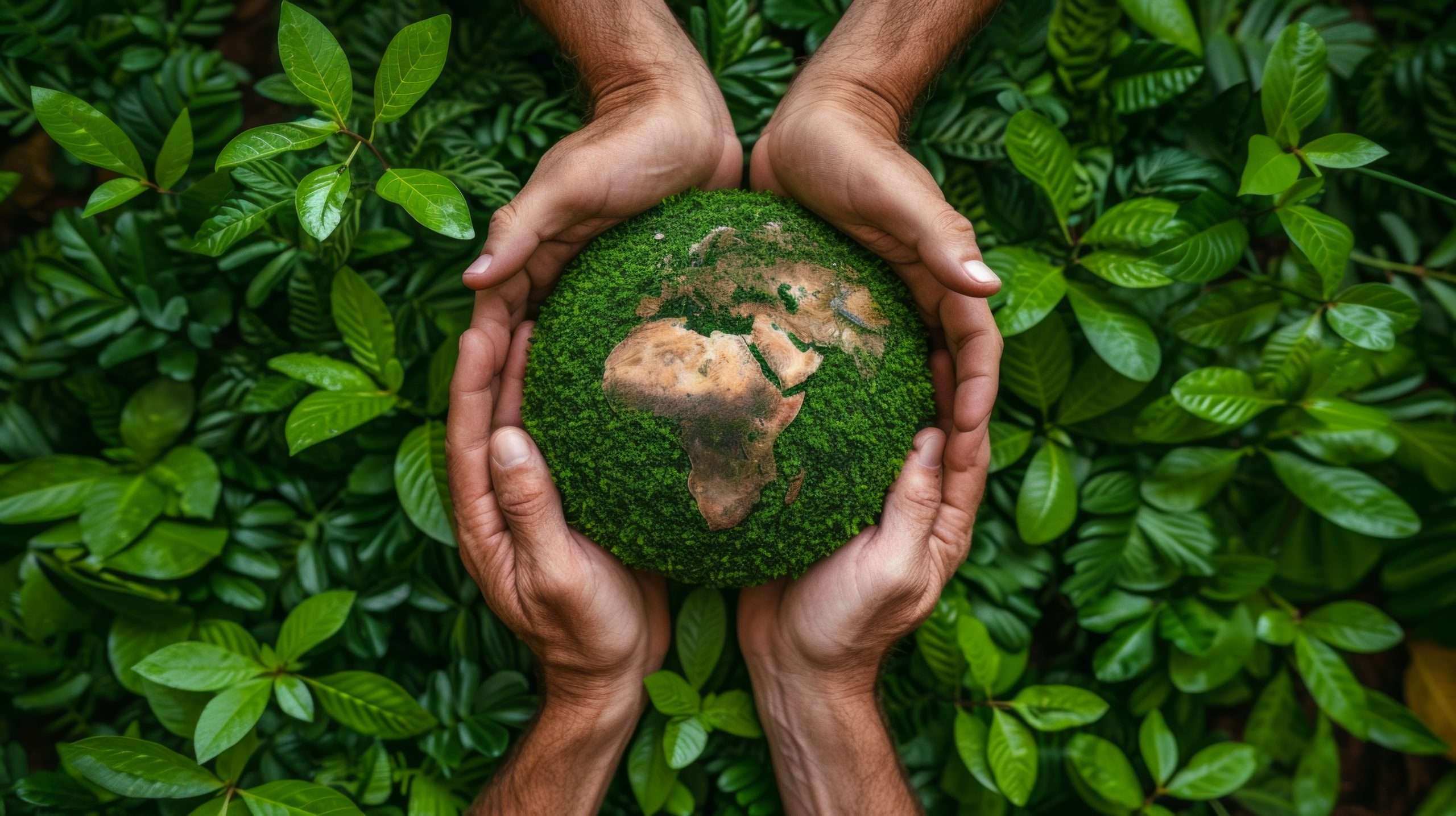

Table of Contents:
- Introduction to predictive maintenance
- Benefits of AI & ML in predictive maintenance
- Implementation challenges
- Case studies
- Future directions
Introduction to predictive maintenance
In the manufacturing sector, the adoption of Artificial Intelligence (AI) and Machine Learning (ML) is revolutionizing operations with unprecedented levels of efficiency and reliability. At the heart of this revolution is predictive maintenance, a technology driven by AI and ML that enables manufacturers to foresee and prevent equipment failures. By harnessing the power of data analytics, businesses can optimize their workflows, reduce downtime, and enhance productivity. As we look ahead, the fusion of AI and ML is set to not only refine maintenance strategies but also transform the overall approach to production and sustainability across industries.
Benefits of AI & ML in predictive maintenance
The adoption of Artificial Intelligence (AI) and Machine Learning (ML) offers multifaceted benefits that revolutionize how manufacturing industries manage their equipment and operations.
Cost Savings:
AI significantly reduces operational costs by minimizing unplanned downtime and optimizing maintenance schedules. According to a report by McKinsey & Company, predictive maintenance can reduce maintenance costs by 10% to 40%, and downtime by 50% to 70% (source: https://www.mckinsey.com/business-functions/operations/our-insights/predictive-maintenance-comes-of-age).
Improved Efficiency:
AI and ML enhance operational efficiency by providing actionable insights derived from continuous data analysis. These technologies monitor equipment performance in real-time, detecting anomalies or deviations from optimal operating conditions. This proactive approach enhances overall equipment effectiveness (OEE) and productivity across the manufacturing floor.
Enhanced Safety:
Predictive maintenance powered by AI contributes to a safer working environment by mitigating risks associated with equipment failures. AI algorithms monitor equipment health parameters, such as temperature, pressure, and vibration levels, to identify potential hazards before they escalate into safety incidents.
Sustainability:
AI promotes sustainability by extending the lifespan of critical assets and optimizing energy consumption. The implementation of predictive maintenance strategies can lead to a reduction in energy consumption by up to 20%, according to the World Economic Forum [source](https://www.weforum.org/agenda/2018/01/these-are-the-top-10-emerging-technologies-of-2018/).
Data-Driven Decision-Making:
AI and ML enable data-driven decision-making, empowering manufacturers with insights into equipment performance trends and maintenance requirements. These technologies analyze historical and real-time data to identify patterns, correlations, and predictive models.

Implementation challenges
While predictive maintenance offers substantial benefits, its successful implementation in manufacturing environments presents several challenges:
Data integration and quality:
Effective predictive maintenance relies on the availability of high-quality data from various sources. Ensuring data accuracy and integrating disparate data streams can be challenging. Robust data integration strategies and governance frameworks are essential.
Skill gap and training:
Implementing AI requires specialized skills in data science, AI algorithms, and machine learning. Addressing the skill gap through training programs or recruiting new talent is crucial.
Infrastructure readiness:
AI systems require robust IT infrastructure capable of handling large volumes of data and supporting complex AI algorithms. Upgrading existing infrastructure may involve significant investments.
Change management and organizational culture:
Introducing AI represents a significant organizational change. Effective change management strategies are crucial to foster a culture of innovation and acceptance of AI technologies within the workforce.
Return on investment (ROI) measurement:
Quantifying the ROI of predictive maintenance initiatives can be challenging. Establishing clear metrics and benchmarks to assess the impact on key performance indicators (KPIs) is essential.
Regulatory and compliance requirements:
Manufacturing industries must navigate regulatory and compliance requirements related to data privacy, security, and industry-specific regulations.

Case studies
Across various industries, organizations are successfully implementing AI-driven predictive maintenance strategies to enhance operational efficiency, reduce costs, and improve asset reliability. Here are a few notable examples:
General Electric (GE):
GE Aviation utilizes AI and machine learning algorithms to predict maintenance needs for aircraft engines. By analyzing sensor data from engines in flight, GE can detect potential issues before they escalate, minimizing unplanned downtime and optimizing maintenance schedules.
Siemens Gamesa:
Siemens Gamesa implements this strategy for wind turbines using AI technologies. By monitoring data from sensors embedded in turbines, Siemens Gamesa can anticipate maintenance requirements and schedule interventions accordingly.
SKF Group:
SKF Group employs AI to enhance the performance and lifespan of industrial machinery. SKF’s Condition Monitoring Center analyzes data from thousands of sensors installed in customer equipment worldwide.
Rio Tinto:
Rio Tinto utilizes AI and predictive analytics to optimize maintenance for its fleet of autonomous haul trucks and drilling equipment. By integrating data from onboard sensors, Rio Tinto predicts component failures and schedules maintenance activities during planned downtime.
Predictive maintenance in automotive manufacturing:
Automotive manufacturers such as BMW and Ford leverage AI-driven predictive maintenance to optimize production line efficiency and ensure consistent quality. AI algorithms analyze data from manufacturing processes to detect anomalies and optimize maintenance schedules.

Future directions
The future of predictive maintenance holds exciting possibilities, driven by advancements in AI, ML, and IoT technologies:
Integration of IoT and Edge Computing:
The integration of IoT devices and edge computing capabilities will enable real-time data processing and analysis at the edge of the network, closer to where data is generated.
AI-Powered Predictive Analytics:
Advancements in AI algorithms will further enhance predictive analytics capabilities. These algorithms will analyze complex datasets with greater accuracy and predict maintenance needs more precisely.
Predictive Maintenance as a Service (PMaaS):
The emergence of Predictive Maintenance as a Service (PMaaS) will democratize access to advanced predictive maintenance capabilities. Cloud-based platforms will offer scalable, subscription-based services.
Digital Twins and Simulation Modeling:
Digital twins will play a pivotal role in predictive maintenance by simulating equipment behavior, predicting performance outcomes, and optimizing maintenance strategies.
Autonomous Maintenance Systems:
AI-enabled algorithms will autonomously trigger maintenance alerts, schedule service interventions, and perform predictive maintenance tasks without human intervention.
Enhanced Predictive Capabilities with Quantum Computing:
Quantum computing holds promise for revolutionizing predictive maintenance by exponentially increasing processing power and enabling complex data analysis.

Conclusion
As manufacturing industries embrace AI and ML technologies for predictive maintenance, the landscape of industrial operations is undergoing a profound transformation. By harnessing the power of data-driven insights, manufacturers can enhance productivity, reduce costs, and improve sustainability. DuckMa is at the forefront of this revolution, empowering manufacturing companies with cutting-edge AI solutions that redefine predictive maintenance practices. The future of manufacturing looks poised to benefit significantly from advancements in predictive maintenance technologies.